
Our Values
It's a values
culture.
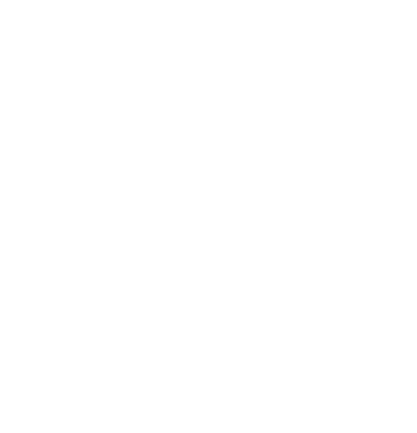
At Alliance Refrigeration Group (ARG), our values are deeply rooted in the commitment to our partnerships and the desire to deliver first-class service in everything we do. Our people-centric culture ensures that we prioritise relationships, transparency, and collaboration, both internally and with our clients. This approach enables us to create bespoke solutions tailored to the specific needs of each project, ensuring that our commercial refrigeration and HVAC systems are not only efficient but also reliable and sustainable.
Manufacturing doors in-house allows us to maintain stringent quality control standards throughout the entire end-to-end process, from design to installation and maintenance. Our team of dedicated design engineers and technicians work closely with clients to understand their unique requirements, providing customised solutions that ensure optimal temperature control, energy efficiency, and compliance with industry standards. Whether it's cold rooms, freezers, chillers, or HVAC systems, our expertise and attention to detail guarantee that we deliver exceptional performance and longevity in every product.
Our long-standing partnerships with clients in sectors such as retail, hospitality, food production, and healthcare are a testament to our commitment to excellence and customer satisfaction. By focusing on preventative maintenance and offering comprehensive service agreements, we minimise downtime and enhance the operational efficiency of our clients' systems. This proactive approach not only ensures the longevity of our installations but also reinforces our reputation for reliability and top-tier service.
At Alliance Refrigeration Group (ARG), our values are deeply rooted in the commitment to our partnerships and the desire to deliver first-class service in everything we do. Our people-centric culture ensures that we prioritise relationships, transparency, and collaboration, both internally and with our clients. This approach enables us to create bespoke solutions tailored to the specific needs of each project, ensuring that our commercial refrigeration and HVAC systems are not only efficient but also reliable and sustainable.
Manufacturing doors in-house allows us to maintain stringent quality control standards throughout the entire end-to-end process, from design to installation and maintenance. Our team of dedicated design engineers and technicians work closely with clients to understand their unique requirements, providing customized solutions that ensure optimal temperature control, energy efficiency, and compliance with industry standards. Whether it's cold rooms, freezers, chillers, or HVAC systems, our expertise and attention to detail guarantee that we deliver exceptional performance and longevity in every product.
Our long-standing partnerships with clients in sectors such as retail, hospitality, food production, and healthcare are a testament to our commitment to excellence and customer satisfaction. By focusing on preventative maintenance and offering comprehensive service agreements, we minimise downtime and enhance the operational efficiency of our clients' systems. This proactive approach not only ensures the longevity of our installations but also reinforces our reputation for reliability and top-tier service.
At ARG, we believe that our success is built on the foundation of strong relationships and a relentless pursuit of quality and innovation. By integrating cutting-edge technology and maintaining high standards across all aspects of our work, we strive to be the preferred partner for all refrigeration and HVAC needs, delivering solutions that meet and exceed the expectations of our valued clients.
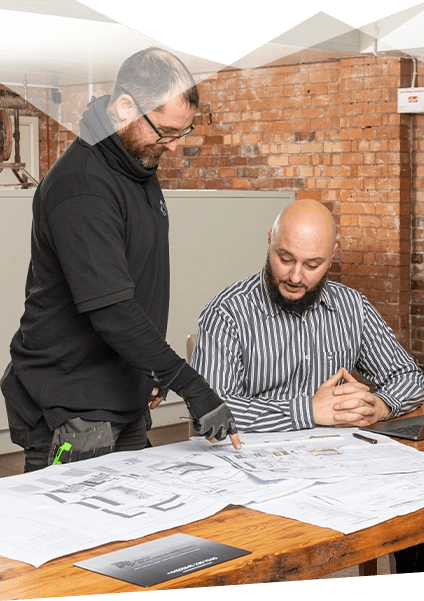
It’s a cutting-edge culture.
"Looking ahead the refrigeration industry, we anticipate
continued advancements in technology, including
advancements in capabilities for remote monitoring and
predictive maintenance."
Mike – Owner & CEO
Call us to start your project today!
Warranty and Quality Guaranteed
Our installations and doors come with a comprehensive 12-month warranty, and optional maintenance plan.
Do you need HVAC for your premises?
We can help. Read about our HVAC installation services
Testimonials
Nadim Hussian
Owner of DIXY CHICKEN LIMITED
Ray Singh
Creative Director
Omar Kayani
Managing Director of KEYANI & SONS LIMITED
Gjergji Shuti
Director of MIMIS KEBABS LIMITED
Martin Borg
Business Owner of MT COLD STORAGE SOLUTIONS
Frequently asked questions
How much does a commercial freezer cold room cost?
What factors affect the price of the refrigeration system?
Is it cheaper to repair or replace my refrigeration unit?
What's included in the cost of an installation?
How do energy efficient refrigeration systems save money over time?
What are the hidden costs for cold maintenance on the refrigeration system?
Do you offer financing options or payment plans?
What are the steps involved in installing a cold room?
How do you handle uneven floors when building a cold room?
What's the difference between a sliding door and a hinged door for a freezer?
How do I choose the right size cold room for my business?
Can you build a custom cold room to fit a specific space?
How long does it take to install a commercial refrigeration system?
What are the insulation options for a cold room?
How do I know what size insulation I need for my cold room?
How do I know if I need a heated floor in my freezer room?
How often should my refrigeration system be serviced?
What's included in a preventative maintenance contract?
What are the most common signs of refrigeration failure?
How can I tell if my cold room is losing efficiency?